Controller Configuration
There are a significant number of control laws, which can be implemented in CNC systems. Typically, any axis control law has two components: the feedforward part which processed the reference position commands, and the feedback part that shapes the measured states such as position, velocity and acceleration to stabilize the closed loop dynamics. The below figure is the axis control law in a standard form.
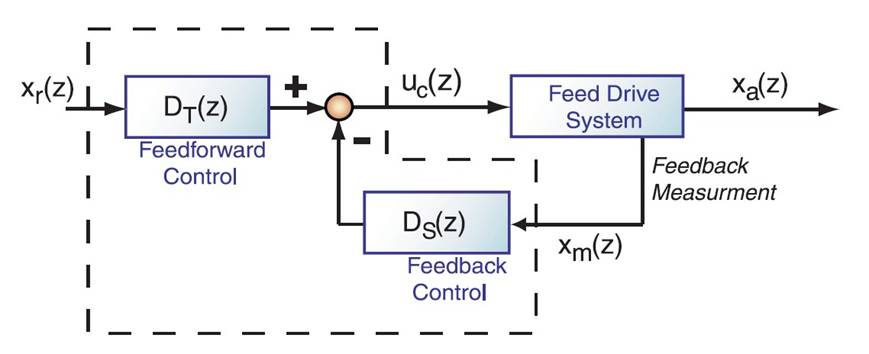
DT(Z) and DS(Z) are the matrices corresponding to the feedforward and feedback transfer functions respectively, in the discrete time domain. Xr(k) is the reference axis command state vector and Xm(k) is the axis measurement state vector.
Virtual CNC has a number of user reconfigurable control law, which have all been experimentally proven on the open CNC system. The conventional control laws include: Adaptive Sliding Mode Control (ASMC), Lead-Lag Control (LLC), Digital Position P-Analog Velocity PI control (P-PI), Digital Position P Control (P), Digital Position PD Control (PD), Digital Position PID Control (PID), Digital Pole Placement Control (PPC), Generalized Predictive Control (GPC) and Feed Forward and Feedback Control (FFFB).
Click the Controller icon in the Axis Servo Drive module, and when the Controller icon is highlighting, you can select different types of controllers by clicking the pop-up menu.
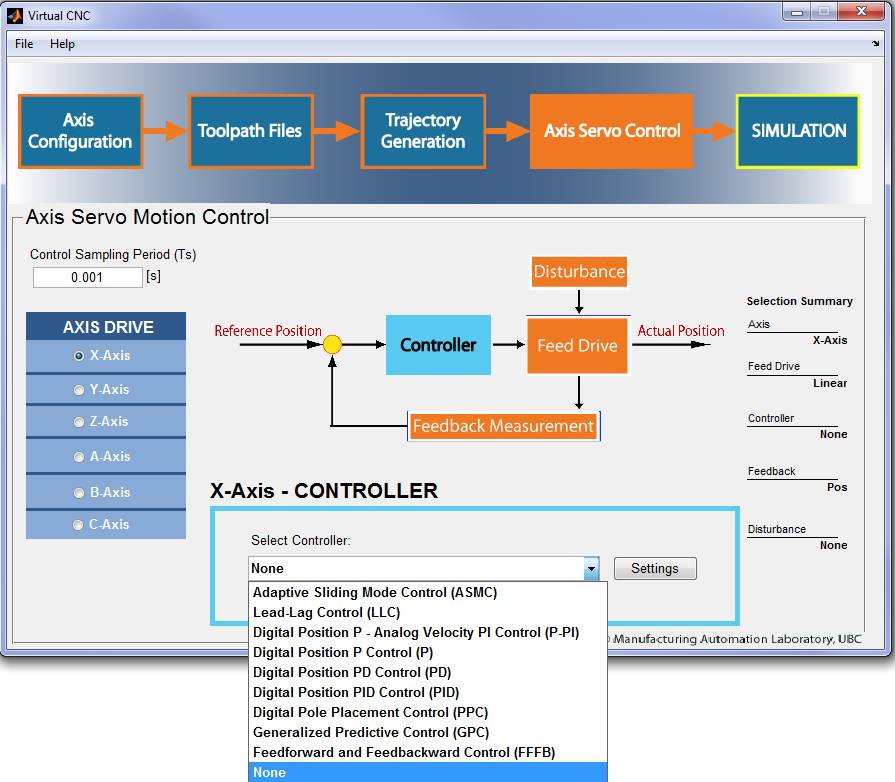
Using the Digital Position PID Control (PID) as an example, by selecting PID option and clicking Settings button, you can set up the PID controller parameters Kp , Ki and Kd .
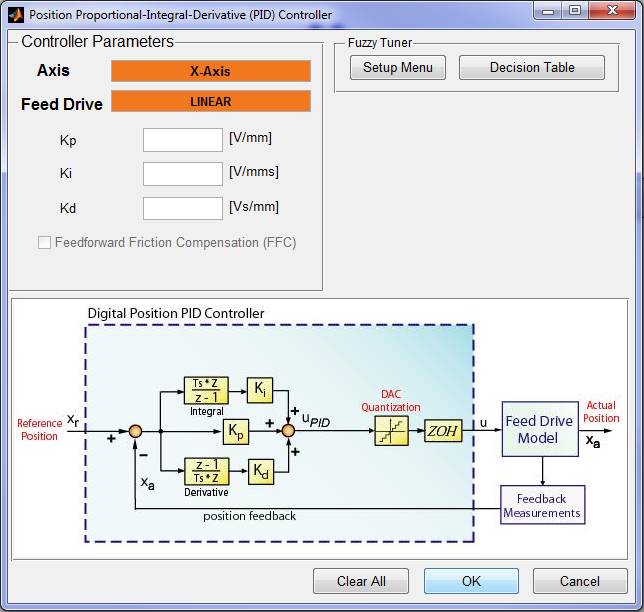
|